ROBOT WELDING GAS REGULATOR AND CONTROLLER
GAS SAVINGS OF 40% FORWARD.
With the VIGILAWELD you will have in only one apparatus:
- A gas flow rate regulator with decimals accuracy.
- A gas flow meter with decimals accuracy.
- A line pressure gauge.
- A torch pressure gauge.
- A totalizer of consumed liters.
- A Welding seams counter.
- A low pressure input gas alarm.
- A high-pressure line torch gas alarm.
- A leaks alarm.
- A consigned set point gas lose alarm .
- A alarm of total liters consumed exceeded.
- A analog output that reflect gas flow rate .
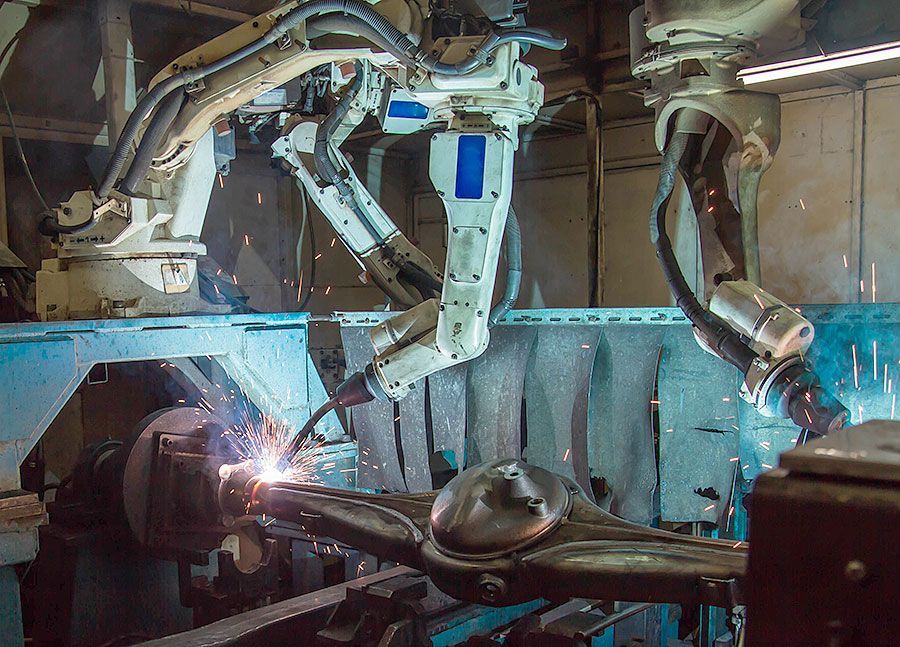
VIGILAWELD CUSTOMER EXAMPLES
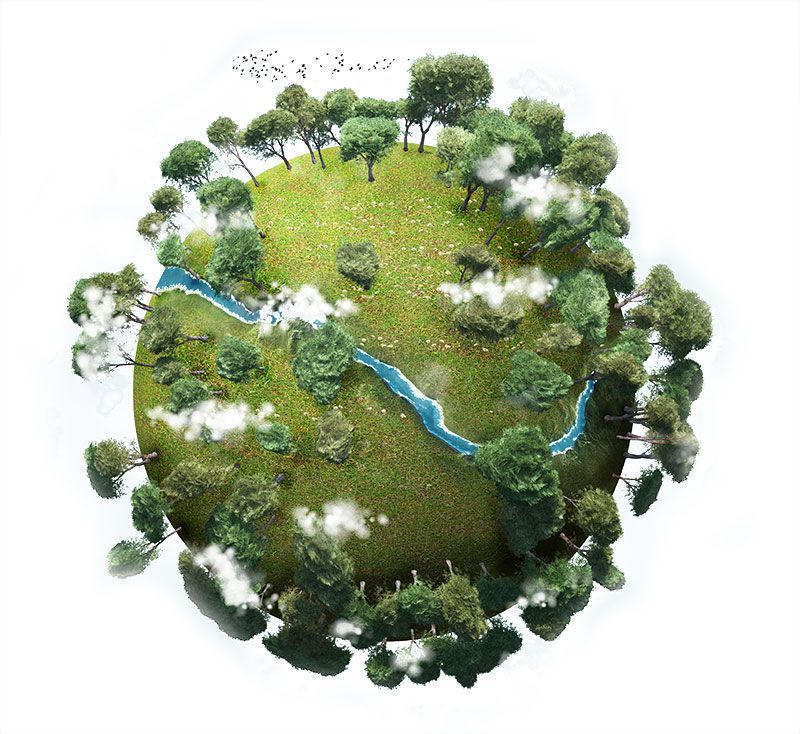
Because we believe in our planet
Saving is not only convenient
SAVE IS NECESSARY
DO YOU HAVE ANY DOUBT ABOUT VIGILAWELD?
The technical team of VIGILAWELD works every day to offer its customers the best information about their products, then you can check the most frequently asked questions, in case you are not in this section your doubt fill out the form and we will contact you you.
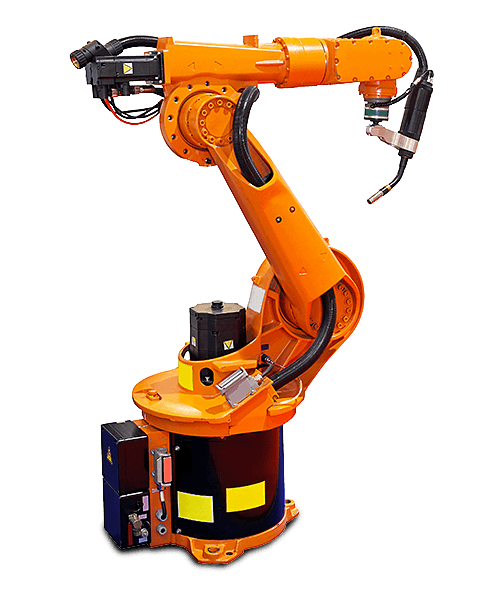
To make a suitable economic approach to implement a VIGILAWELD in a robotic cell we must know the number of daily pieces manufactured , the liters consumed by piece , and the gas cost . An automotive type cell produces around 1000 pieces per day, about 15 liters piece , and 1 or 6 € cost of the m3 of gas if it is of bulk or bottle respectively.
With this data the daily savings can oscillate between from 7 to 40 € .
Before the wire winder valve is opened , the same pressure of the welding cycle is applied ( that can be increased at will ) , which is maintained indefinitely in time , whether or not welding current.
The same as previous welding cycle.
Any welding professional knows that more gas than is strictly necessary is normally used, but he knows he can not lower it because there are a number of uncontrolled parameters in the installation that can, and in fact to do, cause the flow to drops unexpectedly, for example ;
– Instantaneous drop of the line pressure by simultaneous entry of equipment. -down in the pressure of the bottle or the installation when there is lower gas.
-Increase resistance to the gas passage in the power cable and the torch cables by deformations or dirt.
– uncontrolled loses of the torch in some concrete position, etc…
Several coincidences of of these events at the same time can have fatal consequences ….
For all this, it can happen that being everything normal , apparently, we get a seam with symptom of lack of gas, solution? … we heal in health and adjust the flow for excess, .. just in case ….
But this is not here, there is more …
If we need more gas by necessity in a complicated seam, unfortunately we have it in all the work since we can not vary the gas seam to seam as it would be desirable.
IN OTHER WORDS.., THAT WE ADD TO THE UNCERTAINTIES OF THE INSTALLATION THE LACK OF GAS FLEXIBLE CONTROL
The welders also knows that not all cords need the same gas , even though they have the same current, position,
Material, dirt, geometry and position of the area to be welded is very important.
That is why reducing the gas flow required only as a function of current, as other equipment does, is too simplistic.
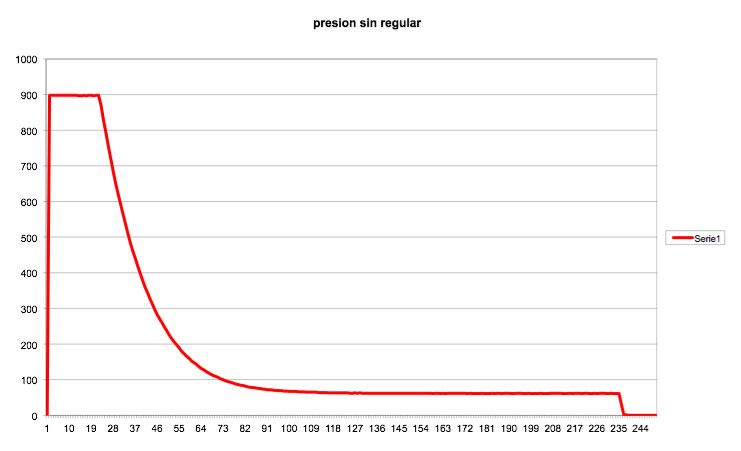
We have another well-known issue;
The excess consumption that occurs in the preflow because the hose remains charged to the line pressure. This, being sincere, with little expense and with a mechanical pressure regulator and rotameter we can avoid it, this is a wise decision and much better than a rotameter with throttle or flow regulator, but we also have to say that in this situation the differences in resistance to the gas passage occurring in the hose from the winder to the torch due to the movement of the robot arm , are not compensated , in any way and unexpected drops in flow can occur.
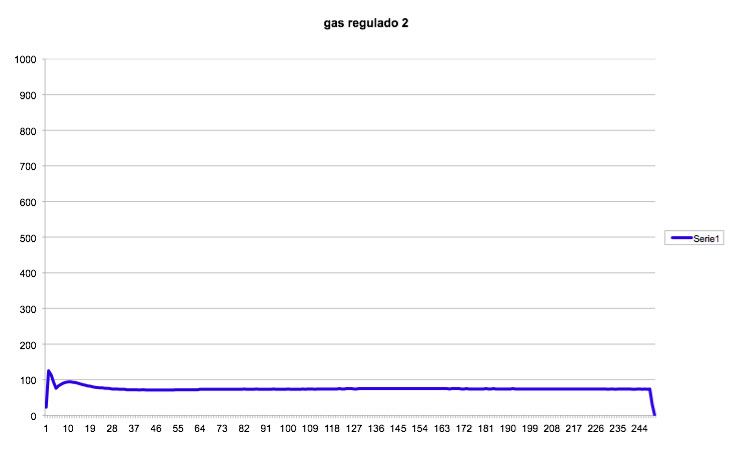
The residual pressure with the WGC1 is reduced to the minimum necessary , and is automatically regulated. There we also have other important savings.
These two graphs are based on the actual gas pressure data taken on the same robot torch from the beginning of the welding, taking ten samples per second, for 10 seconds, in an installation without regular pressure and with regulator WGC1.
It is not an artistic recreation.
Suppose we have a gas installation at 6 bars of pressure we have coupled a rotameter with a regulation tap , or a flow regulator with a Bourdon type meter.(non a pressure regulator)
When the solenoid valve on the winder closes, the entire length of tubing between the flow control valve and the winder is charged to the line pressure, and by experience we know that the pressure required in that section of pipe for 15 liters per minute of Flow rate is normally 0.4 bar.
Therefore at the initial time of the welding there is an excess flow rate and an undesirable consumption which will be equal to the volume inside the pipe multiplied by the difference between 0.4 bar And line pressure, in this case are 5.4 bar above atmospheric pressure. An 8mm diameter inner tube has a capacity of 50 cm3 per meter, with 20 meters in length being 1,000 cm3, or one liter, if we load it with 5.4 bars we have 5.4 liters at atmospheric pressure, each time We make a seam WE TAKE ALMOST FIVE LITERS AND HALF OF GAS.
When more longer and bigger the section of pipeline , will be worse ….
The shorter and frequent are the seams , also worse …
OF COURSE … , that is a fundamental advantage of WGC1 , he can work like a flowmeter and liters totalizer only , without regulation, so can measure the gas that we usually spend for each piece until now , and before , working as a regulator (adjusting the flow to the indispensable by analysis of the welding), remeasure the gas used by piece, is very simple and fast. Without complicated calculations.
WITH TEN OR TWENTY WELDED PARTS we can know exactly how much liters we spend per piece , with or without VIGILAWELD , and calculate just how much we are going to save REALLY ….
YES …, first , WITH THE GAS PASS IN THE SAME POSITION IN WHICH WAS WITHOUT THE VIGILA , we will measure the consumption by setting the WGC1 in flowmeter mode.
When operating the WGC 1 in regulator mode, the GAS PASSAGE must be FULLY OPENED.
The mechanical indicators in this case will not indicate correctly.
One of the objectives we achieve with the WGC1 is the savings, but not the only one, as much or more interesting is the constant monitoring of the welding work as far as the gas is concerned, NOW ..we do not need to check seam by seam to know if the work has been enough gas, if there is a small parameters deviation, we will know immediately before a disastrous weld occurs.
We can set a maximum or minimum alarm threshold to the parameters we measure, each alarm can have several simultaneous actions… display flash, buzzer, relay contact closure ( and / or) gas closing… Actions ranging from the slightest alarm to the most serious alarm.
That is, we can detect anomalous situations by small deviations of the installation pressures and act accordingly automatically, in that sense can also help us as preventive maintenance.
If the gas consumption adjusted in the alarm for the waiting time – between weld and weld – is exceeded, it will notify us. What’s more, if we leave the plant out of service between workdays and forget to close the gas , warn us,and will close the gas, avoiding unnecessary expense.
The controller keeps a screen with the event occurred, even if it disappears, until someone presses the “OK”. You will know what has happened even if the cause of the alarm has disappeared, the welding cell was unattended and nobody noticed anything at the time.
Therefore, a production without alarms is a quality manufacturing lot.
A tenth of bar for the pressures and a tenth of liter / minute for the flows. To achieve maximum precision we will introduce the gas density we are using in the parameters of the apparatus.
We can work with pure gases , like Co2 – Nitrogen – Air – Argon – Oxigen – we can also select one adjustable gas density between 1000 and 2000 gr. M3. Nevertheless it leaves factory calibrated for gases between 1600 and 1800 gr / m3. if you need calibration for another density ask for it when ordering .
Regulates flow rates between 5 and 25 liters / minute.
Between 2,5 an 6 bars …less is not recommendable , although it can work up to 1,5 bar at very low flow rates.
The WGC1 can apply different selected gas flow rates, which may be required by the robot through a combination of digital contact inputs, even change during welding from one to another. You can use up to seven preset WELD-FLOW rates and seven different POS-FLOW rates.
YES…, it has an analog input to which we can connect a voltage output of the robot . Each volt applied to the input is 10 liters / minute. In this way the different flow rates to be applied are unlimited or even generate increasing or waning gas ramps.
In the same way as the robot , or robotic installation , is the one that controls the welding current , now the robot can also adjust the required gas flow , independently of the welding current , with fully flexibility … it can receive the gas setpoint digitally or analog way
Yes… we see not only the gas consigned , but also the actual gas we apply, and the most interesting … we can monitor it automatically because it has an analog output where 1 volt is 10 liters / minute of the REAL FLOW , the robot can check this voltage , and be able to make graphs of each seam or establish parameters of quality control or traceability to the customer.
At all, it is recommended to remove the existing regulator if it is flow rate – scale in liters / minute – especially if it has a Bourdon tube indicator (watch dial with needle). If it is to make comparative test of consumption it can be maintained but opening the step to the maximum with the Vigila as in regulator mode , in that case the measures offered by the mechanical meter or rotameter will not be correct. If it is a pressure regulator what there is – scale in bars – it will suffice to set more than 2.5 bars and prevent anyone from changing it.
In this case it is imperative to put a gas regulator-reducer with manometer , adjusted at least to three bars.
To connect the regulator we only have to place it at any point in the gas installation, before the wire feeder. The necessary electrical connection is through a standard 230 Vac Schuko socket and a 24 Vdc power supply or preferably with a 24 V 1 Amp DC source from the robot. The ground/chassis of the equipment must go to the ground/chassis of the robot and the welding cell. The equipment is convenient to be placed in a visible place to control your screen.
Yes, in normal operation only the two main screens appear and it is not possible to make any configuration changes.
Two years, but we can manage your warranty extension up to five years from the purchase.
SPEAKING CLEAR…
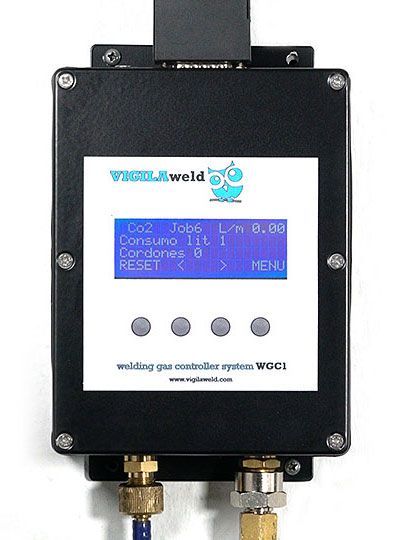
There is one important problem that is very real:
The gas figures advisable in the tables that circulate in technical means are generalist and suffer from the problems mentioned above, therefore to cure in health the flows are quite oversized, very few welding centers lose the time in finding out what the threshold MINIMUN SAFETY FLOW required for a particular weld, because there are no two identical gas installation and , NO EQUIPMENT THAT CAN SUSTAIN THE FLOW WITH GUARANTEES. UNTIL NOW.
ALL THIS CHANGES LUCKYLY WITH THE VIGILAWELD..
With our electronic regulator the selected flow rate is maintained even if the torch pressure can rise dangerously (up to three times normal) or the gas line pressure can drop from 6 bar to 2.5 for example.
Much more …. These variations can be seen in the display and we have alarms before there is a problem in the welding.
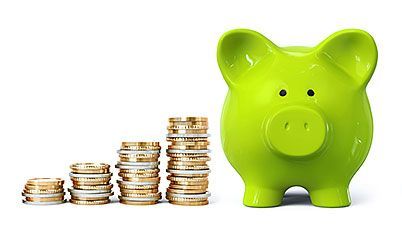
Therefore we can lower the welding flow by 25-30%, even more, compared to the usual rates , because this flow is kept whichever happens in the installation.
To assure the minimum flow rate, we will test several seams by lowering the flow rate until it has an incorrect weld, then we lift them 2 liters / min. , THAT IS THE BEST MINIMUM. If there are complicated seams or critical welds we will test one by one and weld each one with the required flow, no more.
If not done this we are throwing gas and money…
If the work is repetitive and for thousands of pieces…
THIS EFFORT WORTH IT…
CONTACT VIGILAWELD TODAY
If you have any type of doubt fill out the following form, we will answer you soon.
Follow us on social networks
VIGILAWELD through its official distributor is present in social networks, keep up to date with our news